Lección Ocho: Ayuda Mutua de la Industria
El patriotismo de la elite industrial soviética se combinó con la responsabilidad conjunta del resultado final.
La interacción intersectorial en todo momento (en el Imperio ruso, en la URSS y en la actualidad) no pertenecía a las fortalezas de la industria nacional. A diferencia de Alemania o Estados Unidos, donde las obligaciones contractuales han sido y son inmutables y casi sagradas.
Tomemos, por ejemplo, la relación de los metalúrgicos rusos y los constructores de máquinas. En la segunda mitad del siglo XIX, las nuevas plantas de ingeniería de transporte y los astilleros no recibieron la cantidad necesaria de metales industriales de las empresas mineras de los Urales. Este último consideró que no era rentable fabricar una gran cantidad de acero relativamente barato, porque el mismo beneficio proporcionaba una cantidad mucho menor de hierro para techos caro. El metal faltante para ejes de vagones, ejes de motores y revestimientos de barcos tuvo que ser comprado en el extranjero. Sólo a finales de siglo, el problema fue resuelto por las plantas metalúrgicas del sur de Rusia, fundadas por industriales belgas o franceses. En los Urales, los franceses también construyeron una planta - Chusovskoy.
Parecería que en la época soviética no se podía hablar de tales caprichos. Además, las plantas metalúrgicas construidas en los 30 en conjunto proporcionaron metal al país. Sin embargo, cada vez que los fabricantes de maquinaria solicitaron nuevos grados complejos de metal laminado, los metalúrgicos los dominaron durante años o incluso décadas.
Feudalismo departamental
Girar a historias Uralvagonzavod. Ya en sus primeros proyectos, al alcanzar su capacidad de diseño, las ruedas de acero laminado sólido se utilizaron en vagones de cuatro ejes, que estaban previstos para ser suministrados por la cercana planta metalúrgica de Novo-Tagil. Sin embargo, este último fue construido por el departamento metalúrgico, pero transfirió la construcción del molino de ruedas a 1938 - 1942 años, y no en primer lugar. Como resultado, antes de la guerra nunca comenzó. Incluso después de la guerra, el alquiler de ruedas no estaba demasiado interesado en los metalúrgicos. Resultado: hasta la mitad de 50, los autos de Tagil dejaron la fábrica con ruedas de hierro fundido de corta duración en lugar de ruedas de acero. Esto trajo enormes pérdidas para los trabajadores del ferrocarril, pero no había otra opción: ni esos autos, ni ninguno.
Lo mismo sucedió con la introducción de los aceros de baja aleación en la industria de la construcción de automóviles. Prometieron una notable reducción de su propio peso del material rodante, manteniendo todas las características del servicio. Los diseñadores de Uralvagonzavod empezaron a diseñar autos de metal de baja aleación al final de los 30-s, pero su producción en masa comenzó solo en la segunda mitad de los 50-s, ya que los metalúrgicos no dieron los productos laminados o ferroaleaciones adecuados para piezas de fundición.
Hay que decir que el virus del feudalismo departamental también afectó a los constructores de máquinas. En el verano de 1937, tuvo lugar una curiosa historia que caracterizó la relación interinstitucional de la época. La Dirección General de Empresas Metalúrgicas envió un equipo a Uralvagonzavod por cinco mil toneladas de espacios en blanco para el molino de vendas recién encargado de la planta de Novo-Tagil. La Dirección General de Ingeniería del Transporte estaba indignada por la invasión de una empresa subordinada. 11 July, el jefe adjunto de la oficina central de la oficina central G. G. Alexandrov envió una carta a GUMP y a Uralvagonzavod con la siguiente declaración: ni siquiera una copia del atuendo enviado por Uralvagonzavod fue enviada. "Pido establecer un procedimiento firme para emitir espacios en blanco a nuestras plantas solo mediante un acuerdo con nosotros y por medio de Glavtransmash".
Como resultado, en el vendaje de acero, los metalúrgicos fueron presuntamente rechazados debido a la imposibilidad técnica de lanzar lingotes de alta calidad en la tienda de hogar abierto de Uralvagonzavod. Mientras tanto, ya en 1936, se fundió un disco axial aquí, y en 1937, se fundieron lingotes para laminado. Por lo tanto, los lingotes para el molino de vendas, ubicados a pocos kilómetros de la UVZ, tenían que ser transportados desde las plantas de Vyksa y Kuznetsk. Además, la calidad de los mismos dejaba mucho que desear y los volúmenes de suministro eran insuficientes.
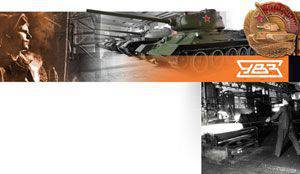
La enfermedad del departamento tampoco perdonó a la industria de la defensa. Numerosas publicaciones sobre la historia de la construcción de tanques soviéticos están repletas de ejemplos de cómo la construcción de prototipos de máquinas o el despliegue de la producción en masa se retrasó debido a la no entrega de metal, especialmente de armaduras.
Incluso hoy, el interés propio de la industria no ha desaparecido, solo ha cambiado su forma. Las solicitudes de nuevas formas de alquiler conformadas simplemente superan los precios exorbitantes. En la política acordada y no se puede hablar. Después del colapso del tipo de cambio del rublo en el turno de 2014 - 2015, las compañías metalúrgicas elevaron los precios del alquiler de automóviles en 30 - 60 por ciento. Y luego comenzaron a quejarse con los fabricantes de maquinaria por el equipo que había aumentado de precio, porque las máquinas se fabrican en Rusia y no están vinculadas a la tasa del dólar.
Parece que en nuestro país solo hay una cura para los problemas intersectoriales: la creación de sistemas integrados verticalmente, donde el mineral extraído con sus propios recursos se convierte primero en metal y luego en máquinas terminadas.
Unidad de guerra
Todavía hay un corto período en nuestra historia cuando los intereses de la industria retrocedieron a un segundo plano. Se trata de la Gran Guerra Patria. El indudable patriotismo de la élite industrial soviética en ese momento se combinó con la responsabilidad conjunta de todos los involucrados en la producción de defensa para el resultado final. Es decir, el director del laminador blindado no era responsable tanto de los volúmenes de acero fundido y laminado como del número de construidos. tanques.
El director del Instituto de Investigación Científica-48, A. S. Zavyalov, dio el primer paso en esta dirección. En los primeros días de la guerra, apeló al gobierno con una propuesta para encomendar al instituto la introducción de tecnologías para la producción de aceros especiales y construcciones blindadas en empresas en el este del país, primero atraídas por la fabricación de vehículos blindados. A principios de julio, una brigada de especialistas de SRI-48 encabezó la reestructuración tecnológica de las empresas más grandes de 14. Entre ellos se encontraban las plantas metalúrgicas Magnitogorsk y Kuznetsk, las plantas metalúrgicas Novo-Tagil y Chusovoy, la planta de construcción de maquinaria pesada de Ural, la planta Krasnoe Sormovo con sede en Gorky, la planta tractora Stalingrad, el octubre rojo de Stalingrad y 264. Así, Zavyalov violó el tabú de antes de la guerra: después de todo, la lista de compañías de tres comisarios estaba en su lista.
El patriotismo y la supresión forzada del egoísmo departamental proporcionaron a la metalurgia soviética tasas de asimilación de productos de defensa sin precedentes, ya sea en el período anterior a la guerra o en la posguerra. En cuestión de meses, en el este del país (principalmente en los Urales), se organizó la producción de ferromanganeso, ferrosilicio, ferrocromo, ferrovanadio y otras aleaciones, sin lo cual es imposible obtener acero para armaduras. Después de la pérdida de las regiones occidentales, la única planta de ferroaleaciones en la URSS siguió siendo Chelyabinsk. En ella, en poco tiempo, la fundición se incrementó dos veces y media. Producido variedades de productos 25, pero sobre todo diferentes tipos de ferrocromo. La fundición de ferromanganeso se estableció en los altos hornos, no solo en los antiguos altos hornos de las plantas de Nizhny Tagil y Kushvinsky, sino también en el gran horno moderno de la cosechadora Magnitogorsk. Al contrario de todas las ideas anteriores a la guerra, el ferrocromo fue fundido en la segunda mitad de 1941, en su alto horno, por los metalúrgicos de las plantas de Nizhny Tagil y Serov, y los científicos de la Rama de los Urales de la Academia de Ciencias de la URSS proporcionaron una gran ayuda para crear la nueva tecnología. Más tarde, dominaron la fundición de ferrosilicio en altos hornos serov.
Antes de la guerra no había campamentos de armadura en los Urales ni en Siberia occidental, debían ser transferidos rápidamente de las empresas en la zona de combate.
En el verano de 1941, el equipo evacuado todavía estaba en camino. Y luego el mecánico jefe del complejo industrial Magnitogorsk, N. A. Ryzhenko, sugirió rodar una armadura en un molino en flor. A pesar del gran riesgo, la idea fue implementada. Y en octubre, el campamento blindado, traído de la planta de Mariupol, entró en operación. Fue montado en 54 del día. De acuerdo con los estándares de preguerra, tomó un año.
La planta de Novo-Tagil consiguió el campamento de Leningrado. La preparación para su recepción comenzó en julio, inicialmente se asumió que se montará en el sitio del vendaje. El campamento de vendas se desmontó, pero resultó que la cama vieja no era suficiente para instalar un campamento blindado y que debía colocarse en otro lugar. La guerra nos obligó a hacer algo que recientemente se consideraba imposible: hace solo un año, los intentos de llevar a cabo una construcción industrial con un método complejo "rápido" tuvieron un éxito parcial en Nizhny Tagil, y en el verano de 1941, la operación de construcción más compleja fue casi perfecta. En septiembre, 10, la primera lámina de acero de Tagil se laminó un mes antes de lo previsto. En total, 13 650 toneladas de chapa metálica se obtuvieron antes de fin de año, incluido aproximadamente el 60 por ciento de la armadura (la fábrica se probó en acero al carbono y, en octubre-diciembre, se desprendió el carbón si no había lingotes de armadura). Como resultado, en enero, 1942, la emisión mensual de placas de blindaje en las fábricas de los Urales superó la mitad de un año en toda la Unión Soviética de antes de la guerra.
Eventos no menos sorprendentes tuvieron lugar en otras empresas poco conocidas. La planta metalúrgica de Zlatoust durante la guerra en términos de fabricación de acero y acero laminado fue inferior a la planta de Magnitogorsk, pero fue significativamente superior a su mezcla de productos: se produjeron aquí las calidades 300 de acero aleado y al carbono. Sin las entregas de Zlatoust, la producción de muchos tipos de armas, principalmente motores de tanques, se detendría.
Las antiguas plantas de Ural eran indispensables en la producción de pequeños lotes de acero especialmente de alta calidad. Por ejemplo, el metal de la planta metalúrgica metalúrgica de Serov, el principal productor de acero calibrado, se invirtió en cada tanque soviético. La planta de Nizhnesaldinsky cambió a la fundición de níquel, hierro fundido y acero. Esta lista puede continuar indefinidamente: durante los años de guerra, donde haya al menos una cúpula, se derritieron armas metal.
Una curiosa historia con flujos para la soldadura automática. Antes y al comienzo de la guerra, fueron fundidos en una de las empresas de Donbass, después de la ocupación de la cual cesaron por completo las entregas centralizadas. Al final de 1941, los empleados del Instituto de Soldadura Eléctrica de la Academia de Ciencias de la RSS de Ucrania comenzaron a buscar materiales sustitutos disponibles en los Urales en condiciones más o menos utilizables. Y los encontraron, en forma de escoria de alto horno de la planta metalúrgica de Ashinsky. Solo se necesitaron mejoras menores: los trabajadores de alto horno enriquecieron sus escorias con manganeso y, por lo tanto, las convirtieron en un flujo bastante adecuado. El equipo necesario para las pruebas fue traído de Nizhni Tagil directamente a Asha.
Muy ilustrativos son ejemplos de cooperación local entre tanques y plantas de acero. Antes del lanzamiento de las capacidades propias, el tratamiento térmico de las partes del tanque de la Planta de tanques de Ural No. 183 se llevó a cabo en la metalúrgica de Nizhny Tagil.
La ayuda de la planta vecina de chamotas Nizhny Tagil, que comenzó a producir tapones refractarios de alta calidad para frenar, contribuyó en gran medida al trabajo exitoso de los trabajadores de la fundición de UTZ. Esto hizo posible producir fundición sin problemas de acero de armadura pesada fundiéndose en piezas moldeadas.
Los hornos de hogar abierto UTZ en 1942 - 1945 trabajaron principalmente en coque y en el alto horno de la planta metalúrgica Novo-Tagil y Ciz y las plantas químicas de Nizhny Tagil. El gasoducto ha operado desde febrero de 1942. La gasolinera propia de la planta número 183 no proporcionó más del 40 por ciento de las necesidades.
A veces un simple consejo era suficiente para resolver un problema. Sobrevive unas pocas semanas antes del inicio del suministro de ferromanganeso sin detener el vaciado de camiones cisterna a la planta número 183 ayudó a la información de los metalúrgicos locales sobre una pequeña mina de manganeso, desarrollada en 1870-s.
Otro ejemplo: con el aumento en la producción de armadura de acero, el taller de hogar abierto no siguió el ritmo de la fundición de metal para los jefes de bombas de aire. No fue posible conseguirlo desde el exterior. El director Y.Ye. Maksarev reprodujo el curso de otros eventos en sus memorias: “Cuando estaba en una de las reuniones en el comité de la ciudad, me reuní con el director de la antigua fábrica de Demidov y me pidió que me quitara los proyectiles de bombas. Él dijo: No puedo ayudar con el acero, pero con un consejo ayudaré. Y cuando llegué a su fábrica, me mostró un convertidor de media tonelada Bessemer de media tonelada. Me dio planos y dijo que sabe que tenemos una buena fundición de hierro mecanizado y que sus convertidores soldarán ”. Así que hubo un pedido para la planta de 8, septiembre 1942 del año, sobre la organización en la tienda de ruedas de la sección de Griffin a Bessemer de tres pequeños convertidores (uno y media toneladas de metal cada uno). El proyecto ya para 25 en septiembre preparó el departamento de diseño y tecnología de la administración de la construcción de la capital, los especialistas del departamento mecánico en jefe soldaron rápidamente los convertidores y las calderas: acumuladores de hierro líquido. Un lanzamiento de prueba de la sucursal de Bessemer y el lanzamiento de un lote experimental de cinco artículos de piezas tuvo lugar en el turno de octubre-noviembre de 1942. A finales de noviembre comenzó la producción en masa.
Al final del tema: la cooperación de metalúrgicos y constructores de tanques en tiempos de guerra actuó en ambas direcciones. Los instaladores de la planta de tanques de Ural participaron en el lanzamiento de muchas unidades nuevas de la planta metalúrgica Novo-Tagil. En mayo, 1944, se produjo un número significativo de placas de revestimiento en el taller de fundición de torres blindadas para reparar el alto horno.
Pero el asistente principal de los metalúrgicos seguía siendo, por supuesto, la planta de construcción de maquinaria pesada de Ural. Los libros de pedidos en UZTM para 1942 - 1945 años están literalmente llenos de documentos sobre la producción de piezas de repuesto y dispositivos para fines metalúrgicos, tanto para las necesidades de la industria de tanques como para las empresas del Comisariado Popular para la Metalurgia Ferrosa. En el otoño de 1942, una unidad especial para la producción de equipos para plantas metalúrgicas se restauró oficialmente en UZTM. Recibió el cifrado "División 15" y estuvo subordinado al subdirector de talleres de adquisición y producción de corpus.
Éxitos en la intersección de industrias.
La cooperación de metalúrgicos y constructores de tanques llevó a la creación de una serie de tecnologías que, sin exagerar, pueden llamarse verdaderos avances científicos y tecnológicos.
Al fundir y enrollar el acero de la armadura en láminas, los metalúrgicos transfirieron sus productos a la producción de cascos blindados. Aquí el metal se corta en un patrón en las partes correspondientes. En la producción de "treinta y cuatro", especialmente una gran cantidad de problemas entregados dos partes del cuerpo: guardabarros (lado inclinado) y la hoja lateral vertical. Ambos eran largos, incluso en franjas anchas con bordes inclinados a lo largo de los bordes.
La idea de hacer rodar una tira de medición de ancho igual a las partes terminadas se hizo evidente. Fue formulado por primera vez por los vehículos blindados de la planta de Mariupol en el verano de 1941. Para el balanceo experimental, elegimos una losa de la cosechadora Zaporizhstal, donde enviamos dos trenes de lingotes de armadura. Pero no tuvieron tiempo de ponerse a trabajar: el avance de las tropas alemanas capturó los dos trenes y también a Zaporozhye.
A la vuelta de 1941 - 1942, durante la evacuación y el dominio de la producción de armaduras en las nuevas plantas, no estaba a la altura de la línea de medición. Sin embargo, en mayo, el 1942-th Commissariat of Ferrous Metallurgy recibió nuevamente una orden de contratación para los tanques T-34 y KV. La tarea no fue fácil: las tolerancias de ancho no deben exceder de -2 / + 5 milímetros, la media luna (flexión) en la longitud total de la pieza - 5 milímetros. Los bordes no permitían grietas, puestas de sol y delaminaciones, por lo que puede soldar sin necesidad de maquinado o corte de fuego.
El trabajo experimental comenzó simultáneamente en los talleres de laminación de las plantas metalúrgicas de Magnitogorsk y Kuznetsk, al principio, sin ningún logro especial. El alquiler de piezas para tanques KV pronto fue abandonado, pero al final el T-34 finalmente tuvo éxito. El grupo de autores, G. A. Vinogradov, Jefe del Departamento Metalúrgico del Instituto de Investigación Científica-48, L. E. Weisberg, Ingeniero Jefe de KMC, y S. E. Lieberman, ingeniero en la misma planta, recibieron una tira cualitativa desde noviembre 1942 hasta enero 1943, utilizando un crimpado. La jaula 900 del raíl y el laminador estructural es un método completamente nuevo de laminación en el borde. En enero, las bandas 1943 se enviaron a 280, en febrero - 486, en marzo - unidades 1636. En abril, después de todas las pruebas requeridas, comenzó el desarrollo de la producción bruta de tiras de medición para defensas de tanques T-34. Inicialmente, se suministraron a UZTM y a la Planta de tanques de Ural, y luego a otras plantas, fabricantes de tanques T-34. El matrimonio, que originalmente era 9,2 por ciento, para octubre 1943 año disminuyó a 2,5 por ciento, además de las tiras fuera de estándar se utilizaron para la fabricación de piezas más pequeñas.
El informe correspondiente del CRI-48 de 25 December 1943 ofrece una evaluación completa y precisa del año: “Se ha desarrollado, probado e implementado en la producción bruta un desarrollo fundamentalmente nuevo, desarrollado para la producción bruta, que se consideró poco razonable hasta hace poco en la URSS y en el extranjero. La recepción de una tira calibrada (dimensional) con el ancho de la parte terminada del casco blindado del tanque T-34 permitió a las plantas NKTP adoptar una nueva tecnología de fabricación de alto rendimiento para detalles de blindaje sin recortar los bordes longitudinales. Debido a la aplicación del nuevo método a uno de los principales detalles blindados del tanque T-34 (guardabarros), se logró un ahorro de tiempo muy significativo (del orden de 36%) al cortarlos. "Ahorro de blindaje de acero 8С a 15 por ciento y ahorro de oxígeno 15 000 m3 en cuerpos 1000".
Al final de 1943, la tira enrollada se dominó para otra parte del casco T-34, la parte vertical del tablero. Solo queda añadir que los autores de esta invención recibieron el Premio Stalin por el año 1943.
En el mismo 1943, los esfuerzos conjuntos de los laboratorios del Instituto Ucraniano de Metales (encabezado por P. A. Alexandrov) y los trabajadores de la Combinadora Metalúrgica Kuznetsk y la Planta de Tanques de Ural desarrollaron y desarrollaron un perfil de producto laminado periódico especial para producir partes masivas y críticas de T-34. Ejes de balanceadores. El primer lote piloto de un perfil periódico se obtuvo en KMK en diciembre, al comienzo de 1944, comenzó la producción en masa. Para octubre, la planta de tanques de Ural había cambiado completamente a la fabricación de ejes de balance a partir de un nuevo blanco, al final del año se unió a UZTM. Como resultado, el rendimiento de los martillos de estampación aumentó en un porcentaje de 63, y el número de averías de la pieza disminuyó.
El éxito de los constructores de tanques fue facilitado en gran medida por los distribuidores del molino de retención de la Planta Metalúrgica Novo-Tagil. A partir de la primavera de 1942, suministraron palanquillas enrolladas con permisos reducidos para el procesamiento, y en 1943, los permisos se redujeron una vez más. Junto con la nueva herramienta de corte, esto hizo posible realizar una extracción de correas de hombro que lleva mucho tiempo estrictamente a tiempo y sin mucho estrés. Un caso más raro: V. A. Malyshev, Comisario de la Industria de Tanques, en su orden de septiembre, 28 de 1943 consideró necesario expresar un agradecimiento especial a los metalúrgicos de Tagil.
Y, por último, el último ejemplo: en 1943, los tanques de soporte T-34 se fabricaron primero en la planta de Chelyabinsk Kirov, y luego comenzaron a fabricarse en plantas especiales de acero perfilado especial. Este éxito también se observó en el orden de V. A. Malyshev.
Queda por añadir que los especialistas de la compañía estadounidense Chrysler, que estudiaron el tanque T-34-85 capturado en Corea, observaron en particular la perfección de los espacios en blanco de acero a partir de los cuales se hizo el vehículo de combate. Y también el hecho de que a menudo superaban los productos de las empresas metalúrgicas de los Estados Unidos.
información